How We Plan to Accomplish This Amazing Feat – Part 2
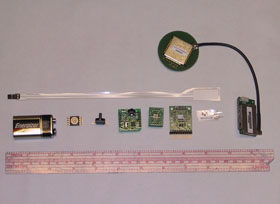
Custom Data Acquisition & Telemetry
To meet the desired resolution, number of inputs, and data rates, we are developing custom-designed and custom-built data acquisition and telemetry systems at Harvey Mudd College. We had student teams in two engineering courses working on the data acquisition and telemetry systems designs for us during the Fall semester of 2006.
Students in the HMC electronics course designed the conditioning and scaling of the analog sensors. The Inertial Measurement Unit (IMU) board and the vibration sensor conditioning board were constructed, tested, and used in the course in Year 0. The IMU board measures three axes of acceleration with MEMS accelerometer chips and three axes of rotation with MEMS rate-gyroscope chips. It also contains an atmospheric pressure sensor for altitude, has connectors for a remotely-mounted differential pressure sensor for velocity measurement, and four remotely-mounted thermistors for temperature measurement. The signal conditioner board conditions the signals from eight (of the sixteen possible) dynamic strain gauges for measurement of the rocket vibration modes during flight.
The vibration sensor signal conditioning boards were populated by our electronics technician and we achieved 100% yield on the eight boards we were able to afford. The IMU boards were more complicated and were sent off campus for population. Ultimately, only two of the eight had all sensors functioning, and the remaining boards had various combinations of accelerometers or rate gyros that did not work. This limitation greatly affected our lab testing and launch schedule.
The initial design of the rocket avionics called for a custom data acquisition system that would sample the IMU, temperature, and pressure data at 1 kSPS per sensor, and also sample eight vibration-sensor channels at 20 kSPS per sensor. It would also integrate GPS data and data from a three-axis magnetometer. The data would be stored on board and also downsampled and sent at 10 SPS per sensor to the ground via telemetry. Our objective is to assign a rocket to each team for the entire semester; the team would characterize only that rocket and associated electronics in their lab experiments. Some preliminary design of the digital side of the custom data acquisition system was done by a student team in the HMC microprocessors course during the Fall semester of 2006. The design has gone through several iterations.
Our current plans involve completing the design and prototyping of the custom data acquisition and telemetry system, which has grown to two boards: one purely for high-speed data acquisition for the vibration sensors, that can be used with either the R-DAS or the custom DAQ, and another a custom low-speed DAQ for the remaining sensors, a GPS, a three-axis magnetometer, a telemetry transmitter, and substantial processing power for data analysis. The design and prototyping of the second board may not be finished by the end of Summer 2008.
We also plan on getting the boards made for additional IMUs, vibration signal conditioners, and the high-speed DAQ boards and having them populated.
If time permits, we will do the same for the low-speed DAQ with telemetry. The currently envisioned design is based on Analog Devices Blackfin ADSP-BF537 microcontroller and programmed with National Instruments LabVIEW for Blackfin software. It would acquire 16 channels of low-speed (2 kSPS) 16-bit analog data (6 channels from the 6-DOF IMU, four from the thermistors, one each from the pressure-altitude sensor and the Pitot-static sensor, two for monitoring battery power, a lesson learned from the destroyed rockets, and 2 unspecified) and store them on a 1 GB MicroSD card. It would also acquire and store data from a GPS, and from a 3-axis magnetometer. A processed subset of the data would be sent to a 900 MHz telemetry transceiver (the TI CC1101 chip) and beamed to the ground. It would also perform the R-DAS functions of detecting liftoff and deploying recovery at apogee.Please continue reading about our Experiment Design.